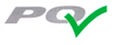
UVISON has been involved in the validation of analytical instrumentation since 1996. The key factor in the successful PQ of analytical instrumentation is the use of qualification methods which are traceable to nationally recognised standards.Using an independent PQ provider eliminates the cost of training and the requirement for expensive calibration reference standards and equipment. All the standard modules of an chromatography system are covered by the UVISON independent PQ, including, detectors, solvent delivery systems, sample injectors, data systems, integrators and chart recorders and many more.
Nationally Traceable Liquid Standards
You can perform your own PQ on any type of chromatography detector using nationally traceable liquid standards in full compliance with GLP, FDA ISO 9000 GMP and other regulatory requirements. The standards can be used to check wavelength accuracy and absorbance linearity, traceable back to NPL the UK standard. Liquid standards cover UV/Vis, diode array, refractive index and fluorescence detectors.
Regulatory Perspective on PQ
Traceability of standards, ISO-9000- clause 4.11
"...the user shall identify, calibrate and adjust all inspection, measuring and test equipment and devices that can affect product quality at prescribed intervals, or prior to use, against certified equipment having a known valid relationship to nationally recognised standards"
Use of an independent approved service agent
This is reinforced by the UK Organisation of Pharmaceutical Analysts, the PASG, who in their paper (Pharm. Tech (Europe), p40-46) state;
'It is likely that the planned non-method specific checks will most conveniently be carried out by the manufacturer (or approved Service Agent) immediately after the routine service."
Roles and responsibilities of an independent approved service agent
-
The ability to PQ all manufacturers' instruments
-
Full, proven and detailed operational procedures
-
Nationally traceable calibrators and standards
-
Formal certificates of successful PQ - produced on-site (as shown below)
-
Traceably trained PQ engineers
-
Independence of OEM's and user company
The intended purpose of Performance Qualification is to demonstrate compliance with all requirements given in the User Requirements Specification document. Performance Qualification should follow on from successful completion of Operational Qualification (OQ) and should include tests designed to verify the satisfactory performance of the equipment or system in the organisations processes. Performance Qualification should be carried out using real process materials and tests intended to demonstrate satisfactory performance over the full range of expected operating conditions.
Prior to Performance qualification; all required methods and Standard Operating Procedures should have been finalised and operator training completed. Also, requirements for Calibration, Preventative Maintenance and Cleaning should have been addressed. Performance Qualification is the last of the Qualification processes and should only commence after successful completion of Operational Qualification (OQ).
Performance Qualification is best performed by the personnel who will be responsible for the routine operation of the system; the users must have received full training on the correct operation of the equipment or system prior to conducting PQ. Standard Operating Procedure (SOP)s must be written prior to start of PQ and followed at all times during the operation of the equipment or system.
Where a system is to be used in a single process, then PQ may be a single one-off exercise, manufacturing a predetermined number of product batches to demonstrate consistent correct performance. Alternatively and more usually, PQ may be a continuous ongoing activity throughout the operating life of the system, intended to show the continuing correct performance of the equipment or system as changes are made to the system or equipment or to the process or materials that interact with the system.